Getting your hospitality business ready to sell
Selling a hospitality business is a significant step that requires careful planning and preparation.
Whether you run a hotel, restaurant, café, or bar, making your business appealing to potential buyers can significantly increase its value and help you achieve a successful sale. Here’s the six areas we believe you need to focus on to prepare your hospitality business for sale and enhance its appeal to buyers:
- Organise your financial records
- Optimise your operations
- Build a strong brand and reputation
- Review and upgrade your physical assets
- Strengthen your team
- Get professional advice
Let’s explain each further.
1. Organise Your Financial Records
One of the first things potential buyers will want to see is your financial records. Clear, accurate, and up-to-date financials are essential for demonstrating the profitability and stability of your business.
- Clean up your books: Ensure all financial records, including profit and loss statements, balance sheets, and tax returns, are accurate and well-organised. Ideally, you should have at least three years of financial records readily available.
- Show consistent profitability: Buyers are looking for a business that generates consistent profits. If your financials show steady growth or a stable profit margin, you’ll have a stronger negotiating position.
- Reduce personal expenses: If you’ve been running personal expenses through the business, now is the time to separate them. Buyers want a clear picture of the business’s true profitability.
2. Optimise Your Operations
Streamlining your operations not only enhances the appeal of your business but also makes it easier for a new owner to take over.
- Standardise procedures: Document your operational procedures, from employee training to customer service standards. This makes it easier for a new owner to maintain the quality and consistency of the business.
- Improve efficiency: Look for ways to cut costs and improve efficiency. Whether it’s renegotiating supplier contracts or implementing energy-saving measures, small improvements can add up and make your business more attractive.
- Enhance technology: If your business is not already using modern technology for bookings, inventory management, or customer relations, now is the time to invest. A tech-savvy operation is more appealing to buyers looking for a business with growth potential.
3. Build a Strong Brand and Reputation
A strong brand and reputation are invaluable assets in the hospitality industry. Buyers are looking for businesses with a loyal customer base and a positive public image.
- Invest in marketing: If you haven’t already, develop a robust marketing strategy that highlights your business’s unique selling points. This could include social media campaigns, partnerships with local influencers, or special promotions to boost visibility.
- Maintain high standards: Ensure your business consistently delivers high-quality service. Positive reviews and word-of-mouth recommendations can greatly enhance your business’s appeal to buyers.
- Create a memorable experience: Consider ways to create a unique and memorable experience for your customers. This could be through special events, themed nights, or offering something that sets your business apart from competitors.
4. Review and Upgrade Your Physical Assets
The physical condition of your premises and equipment plays a crucial role in the sale process. Buyers are more likely to be attracted to a well-maintained, up-to-date business.
- Conduct a thorough inspection: Review the condition of your premises, equipment, and furnishings. Address any maintenance issues and consider upgrading outdated equipment or décor.
- Enhance curb appeal: First impressions matter. Make sure your business’s exterior is clean, inviting, and well-maintained. A fresh coat of paint, updated signage, and tidy landscaping can make a big difference.
- Review lease agreements: If your business operates from leased premises, ensure your lease agreements are in good standing. Buyers will want to know that the business can continue operating without immediate lease issues.
5. Strengthen Your Team
A strong, reliable team is a valuable asset to any hospitality business. Buyers want to know that they can count on the existing staff to maintain operations during and after the transition.
- Train and retain key staff: Identify key staff members and ensure they are well-trained and motivated to stay with the business. Offering incentives or bonuses can help retain top talent during the sale process.
- Develop a succession plan: If you are heavily involved in the day-to-day operations, consider how the business will function without you. Developing a succession plan, or delegating responsibilities to key staff, can make the transition smoother for a new owner.
6. Get Professional Advice
Preparing a business for sale can be complex, and it’s often worth seeking professional advice to maximise your results.
- Hire a business broker: A business broker with experience in the hospitality industry can help you navigate the sale process, from valuation to negotiations and closing the deal.
- Consult with an accountant: An accountant can help you organise your financial records, identify tax implications, and advise on ways to structure the sale for maximum financial benefit.
- Legal consultation: Ensure all contracts, leases, and legal documents are in order. A lawyer can help you address any potential legal issues that could arise during the sale process.
Conclusion
Selling your hospitality business is a significant decision that requires careful planning and attention to detail. By organising your financials, optimising operations, building a strong brand, and seeking professional advice, you can enhance your business’s appeal to potential buyers and achieve a successful sale. Remember, the more prepared you are, the smoother the process will be, leading to a better outcome for both you and the buyer.
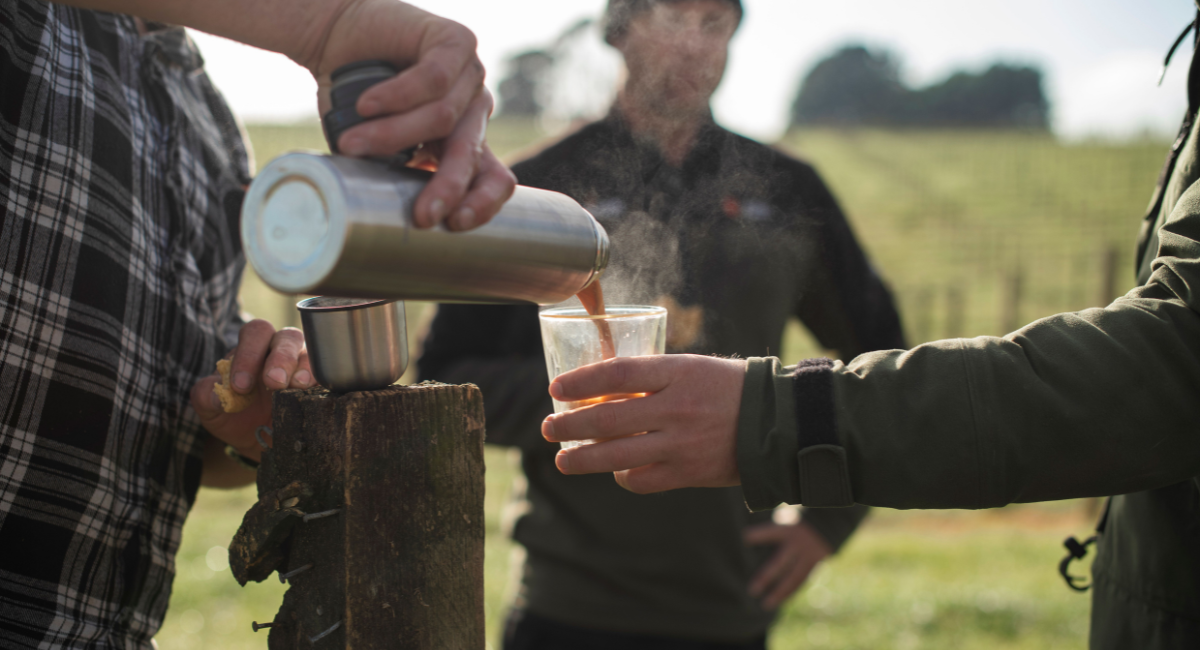
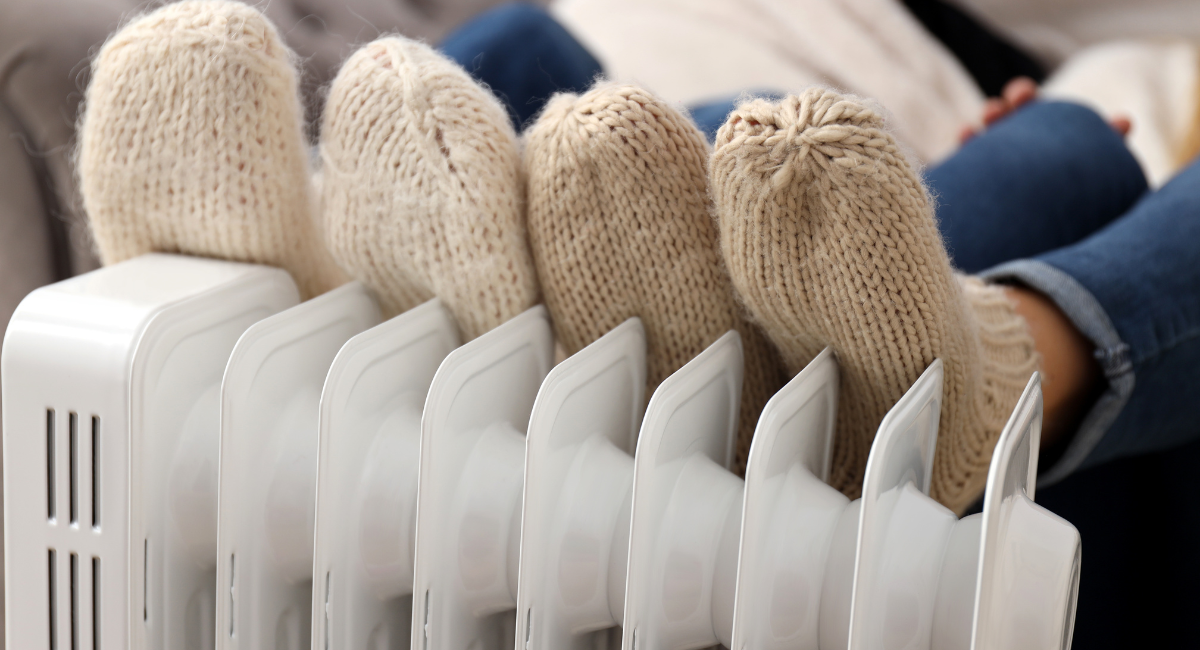
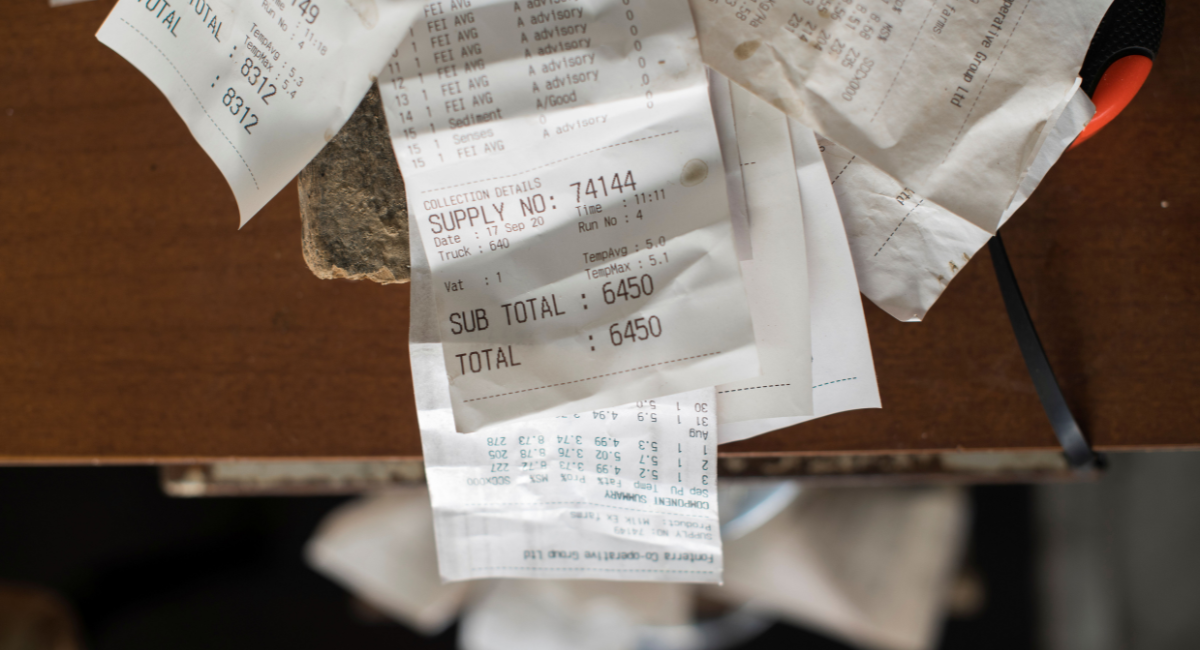
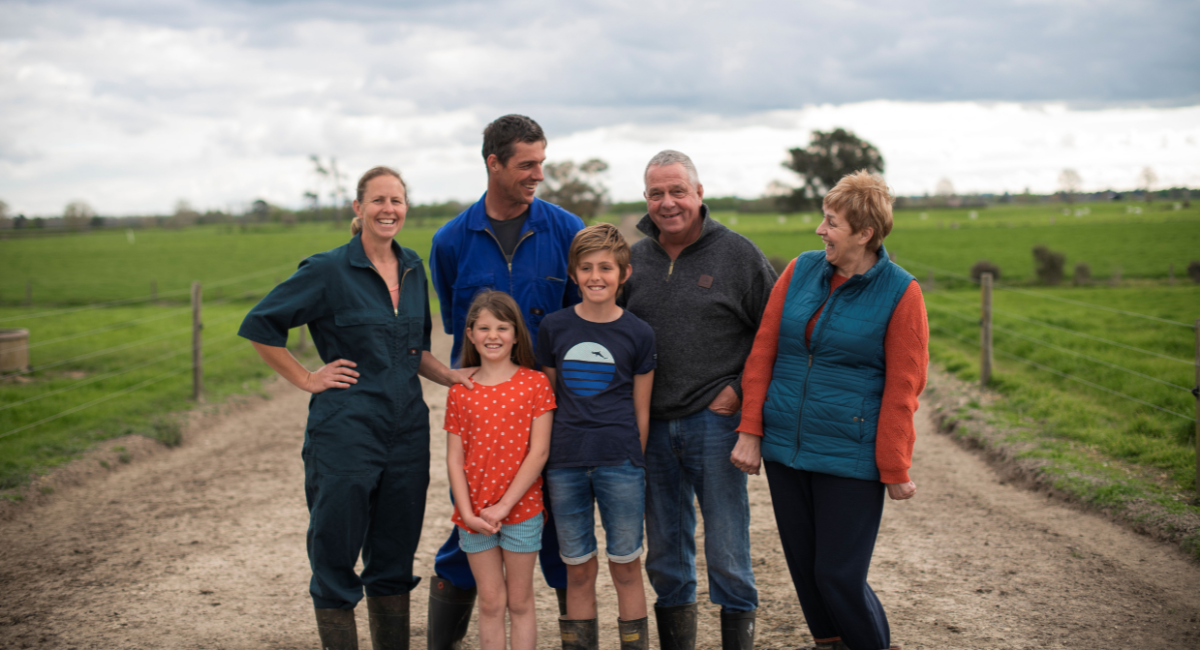
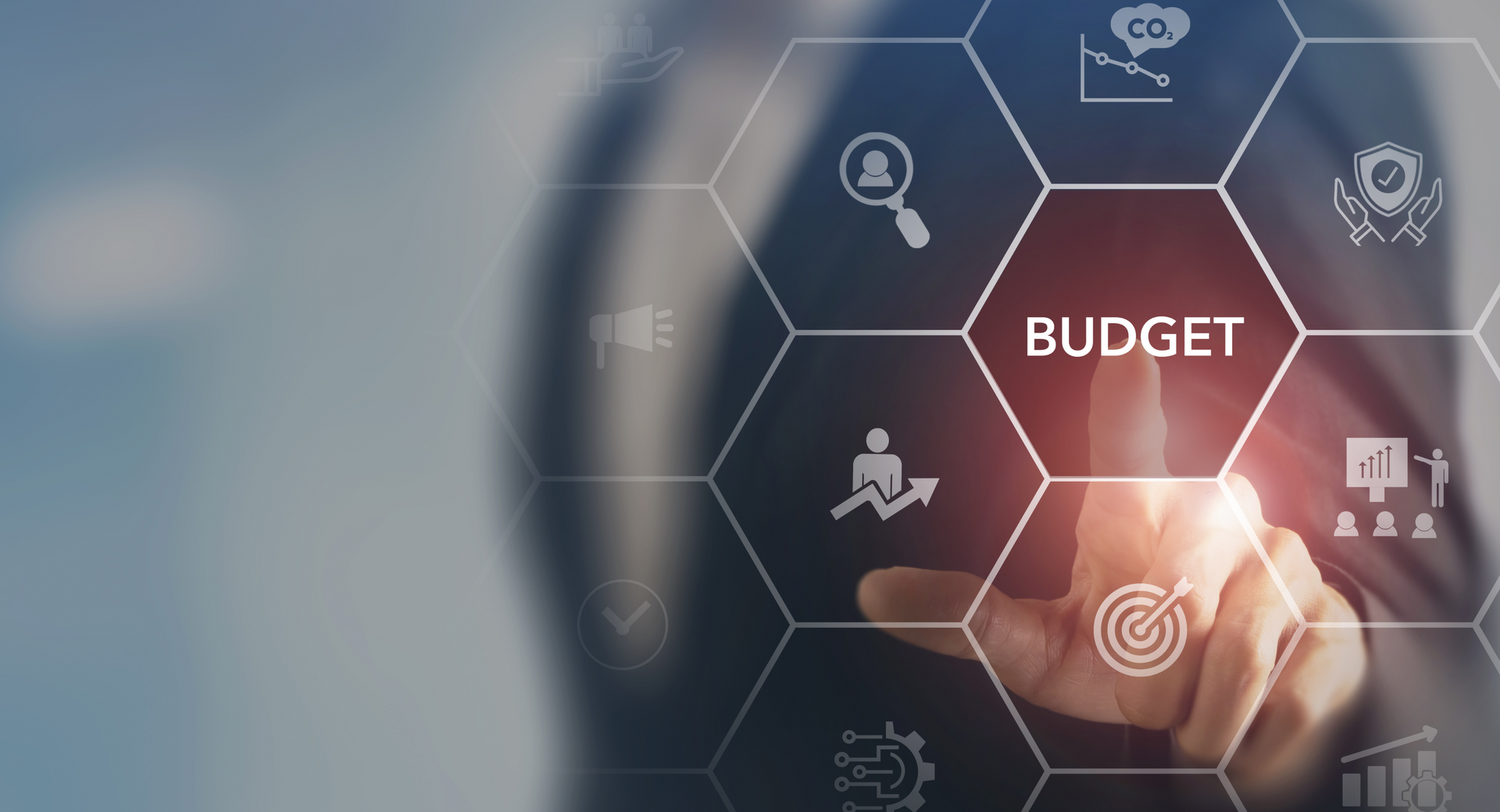
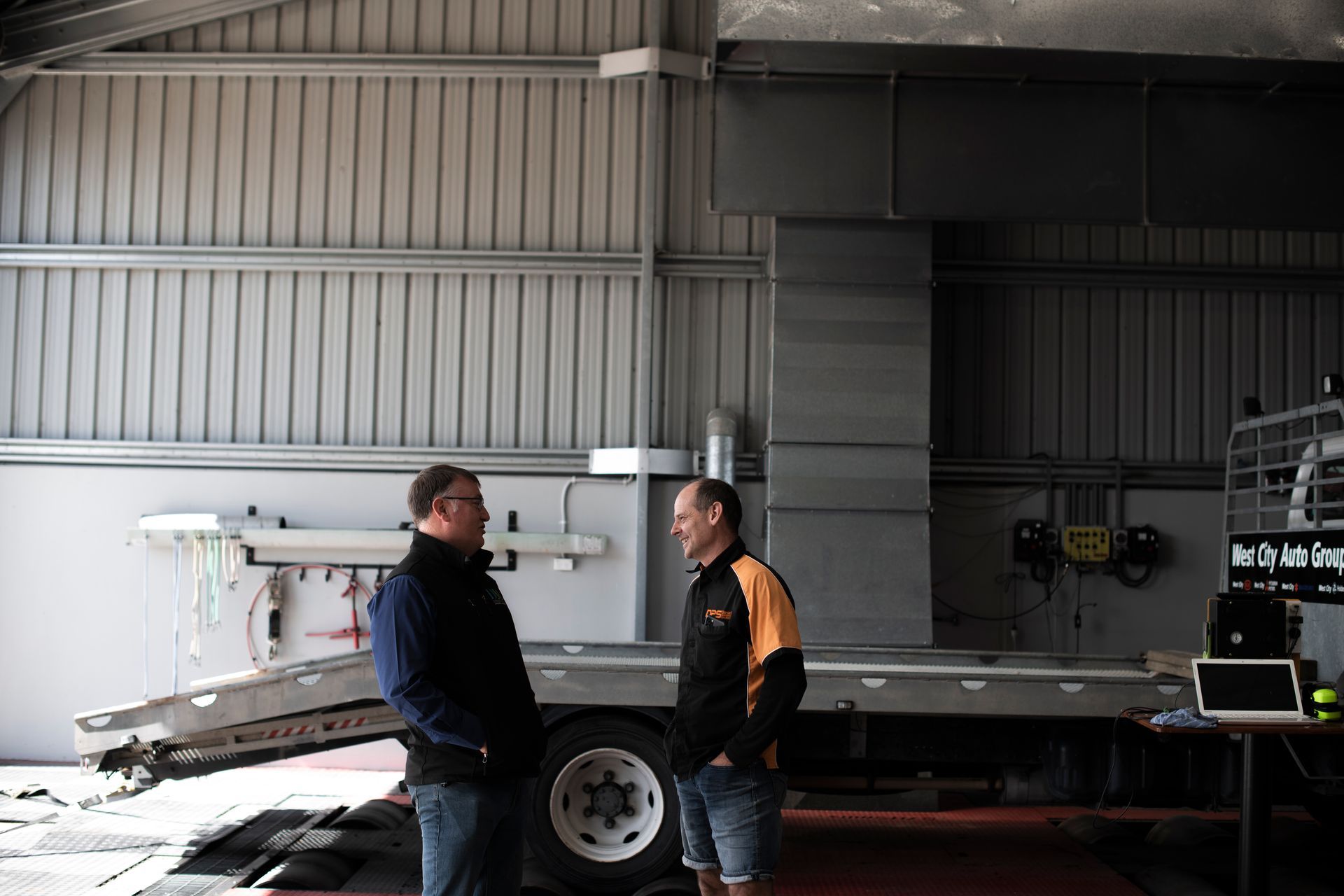
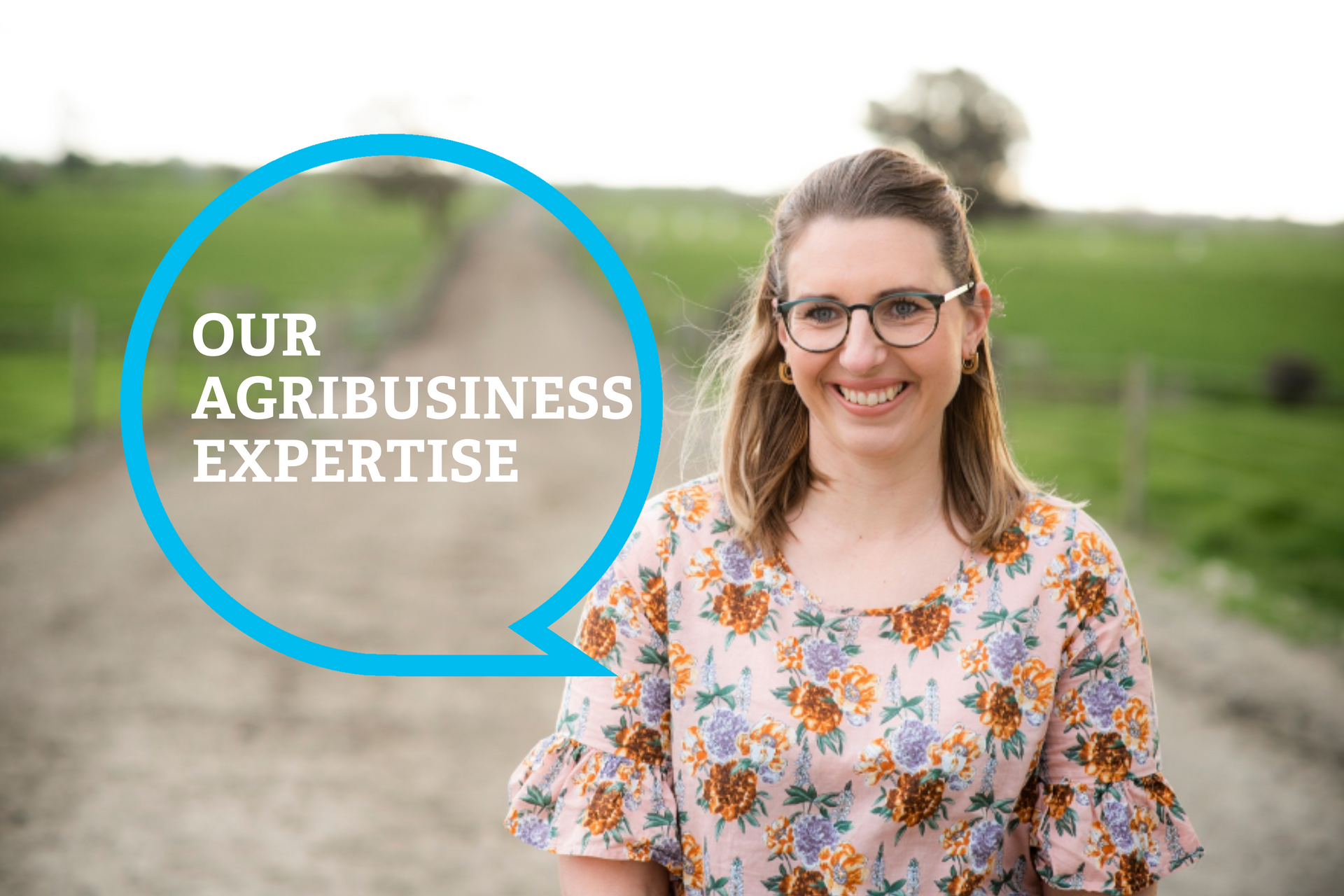
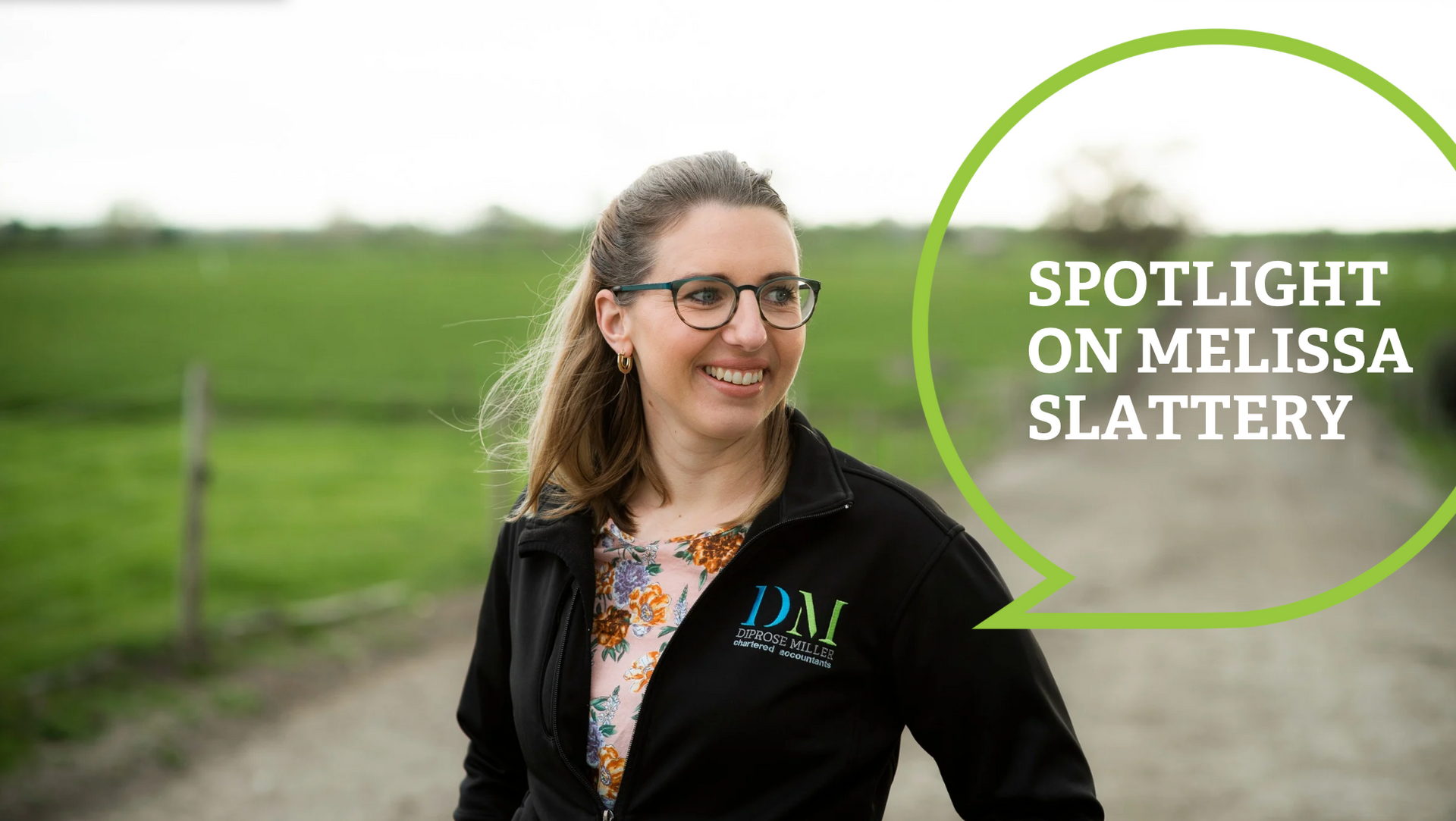
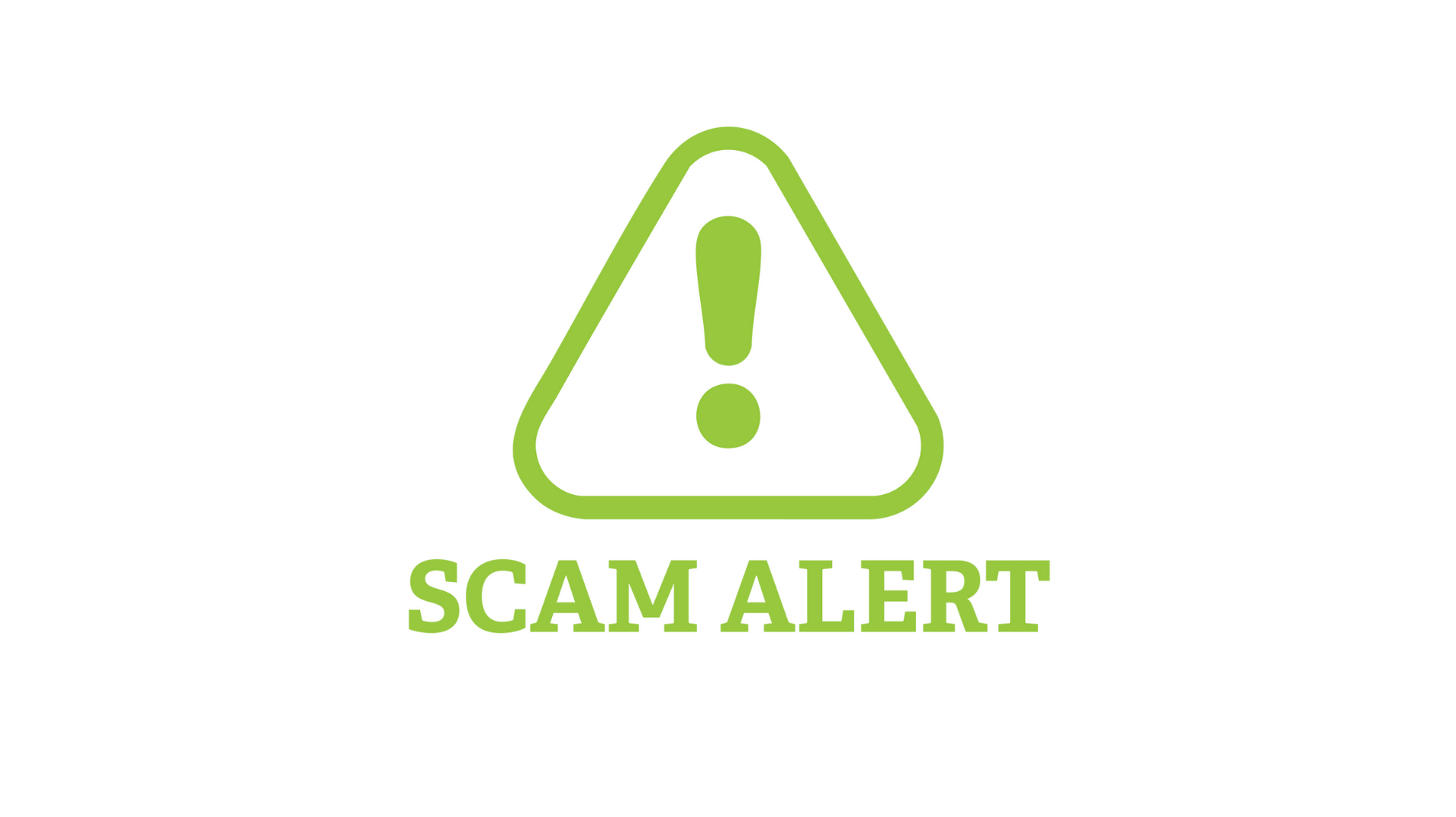
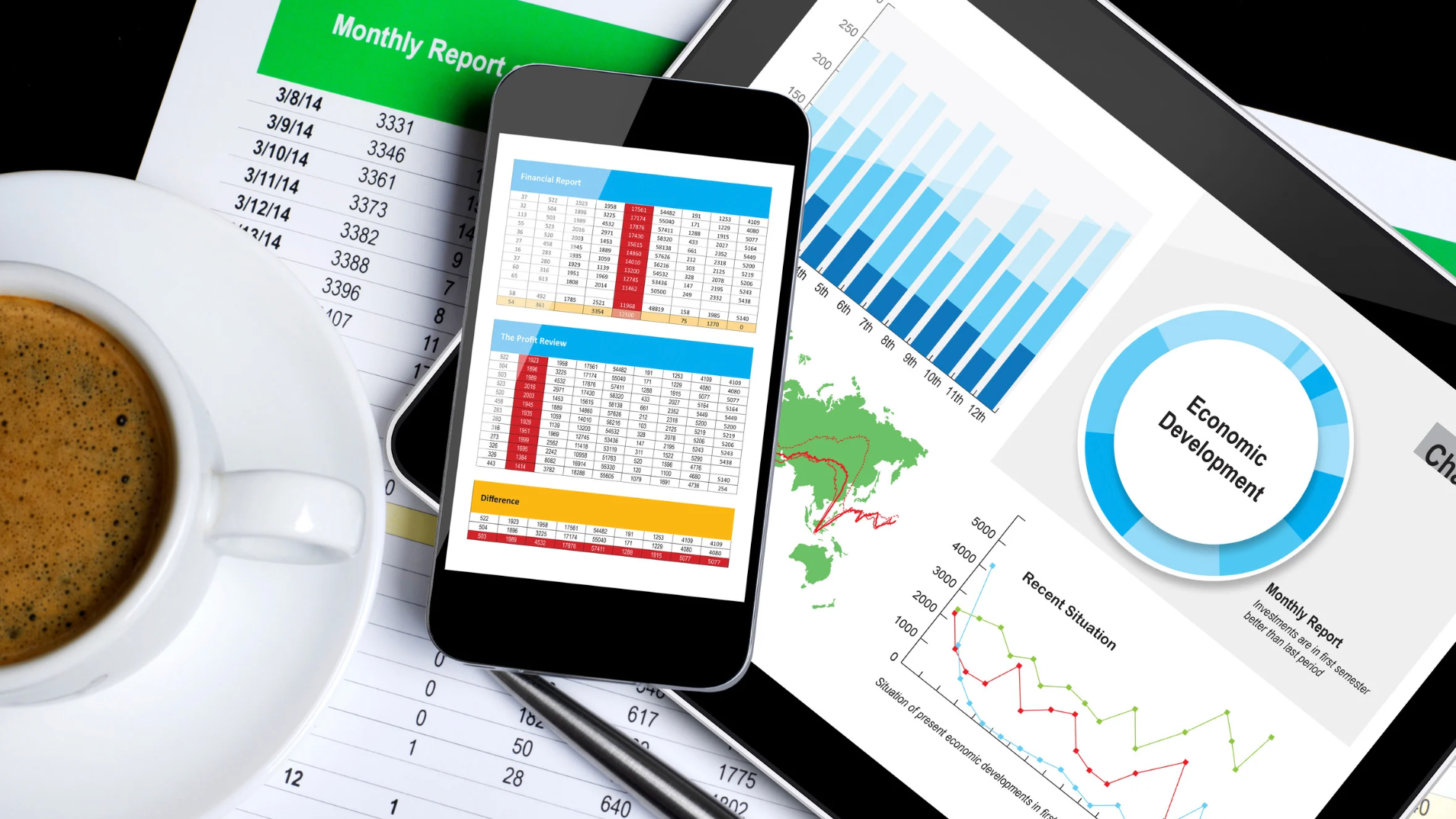